The importance of digitalization in production is constantly growing. According to a Bitkom study, 86 percent of companies consider robotics to be of high or very high relevance and as many as 91 percent of the companies surveyed say that Industry 4.0 and digitalization are essential in order to survive in international competition. Nevertheless, many companies are cautious when it comes to implementation: although the industry has recognized the potential of digitalization and has very positive expectations of its impact, less than half of companies are using digital technologies such as robotics (40%) or the Internet of Things (36%).
Finding digital solutions that are a perfect fit
ConMoto supports companies in making the right decisions. Not every digital innovation automatically leads to a competitive advantage. Digital solutions must always be considered in the context of actual needs. For example, automated quality assurance processes or data-based decision-making often offer significant advantages, while other solutions only generate costs in certain scenarios. Small and medium-sized companies need to evaluate their investments particularly carefully. A fully digitized “smart factory” system can be more of a burden than a benefit for SMEs, while it generates enormous efficiency gains for large corporations. In addition to being cost conscious, we work with our customers to consider aspects such as scalability, flexibility and integration capability in order to obtain a holistic picture as a basis for decision-making.
Digitizing manufacturing and production: Important technologies and trends
A variety of technologies offer great potential – but not every technology is suitable for every company. The most important solutions include
- IoT (Internet of Things): Machine networking for real-time data exchange and transparent processes.
- Artificial intelligence (AI) and machine learning: Optimization of production and predictive maintenance to minimize downtimes.
- Automation and robotics: Precise, efficient production and reduction of manual tasks.
- Digital twins: Virtual models for simulating and optimizing production.
- Manufacturing Execution Systems (MES): Integration and control of the entire production chain.
- Cloud computing: Scalable data infrastructures for analyses and reports.
- Process Mining and Big Data Analytics: Uncovering optimization potential through comprehensive data analysis.
- Single source of truth/transparency: Data-lake with company-wide standardized data for data-based e2e transparency.
ConMoto’s pragmatic approach to digitalization
A pragmatic approach prevents digitalization strategies from failing. We develop digitalization solutions that do not overburden companies and offer added value that brings cost benefits and productivity gains. A structured approach helps on the way to the goal:
- Needs analysis: We analyze existing processes, identify challenges and avoid developing technological solutions that are not adequate to the problem.
- Individual requirements profile: Using proven best-practice approaches based on the evaluation of numerous projects, we develop tailor-made digitalization solutions.
- Pilot projects: We test the use of new technologies on a limited scale before major investments are made.
- Focus on profitability: Every investment is underpinned by a detailed business case and must deliver measurable added value.
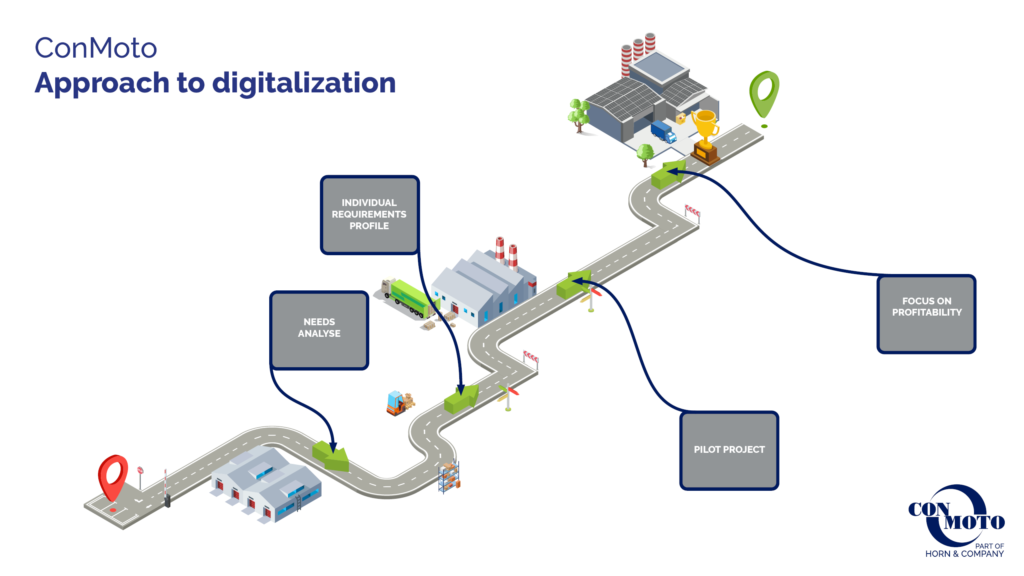
The three key benefits of digitalization
Digitization is so effective in improving competitiveness because it not only helps to reduce costs, but also increases the efficiency of production systems. The three key factors here are:
- Cost reduction: Less material wastage, lower warehousing costs and shorter throughput times significantly reduce costs. 81 percent of companies expect digitalization to be the most important lever for greater sustainability.
- Greater flexibility: Faster adaptation to market changes and individual customer requirements ensure increased competitiveness.
- Increased efficiency: Automated and data-driven processes optimize production workflows and avoid delays. 61 percent of companies say that digitalization makes work less error-prone
Success story: Smart factory for an automotive supplier
An informative example is the planning of a greenfield plant for a medium-sized Tier 1 automotive supplier. In view of stable global growth, the task was to create additional capacity for supplying new customers. The analysis produced a business case for adapting the footprint strategy and building a new plant in Poland. This Factory of the Future should meet the highest standards of automation and digitalization.
Together with the customer, ConMoto evaluated several possible alternatives. The decision was made in favor of a tailor-made approach that enabled the integration of state-of-the-art digital solutions without getting bogged down in oversized technological gimmicks. After intensive analysis, a semi-automated painting system proved to be more cost-efficient and flexible than the originally planned fully automated solution – with a shorter amortization period, greater scalability and better results in terms of sustainability. In addition to the semi-automated solution for the paint application, other concepts such as the Internet of Things, MES, traceability using RFID, production planning based on Heijunka and e-Kanban-controlled material provision were designed and implemented. With this smart factory, the automotive supplier was able to compensate for the 15 percent increase in labor costs and at the same time meet its ambitious targets for quality and production flexibility.
Our view of digitalization – targeted and strategic
Digitalization is an opportunity – but only if it is approached correctly. It’s not about blindly following the latest trends, but using the technologies that offer real added value for your company. We support you in finding the right path. Contact us to approach your digital transformation with a clear focus.